The Cost of Poor
Power quality
The Electric Power Research Institute estimates that U.S. businesses lose between $119 and $188 billion per year as a result of poor power quality; the numbers are similar in Europe, with an estimated €150 billion lost each year, according to the Leonardo Power Quality Initiative. These losses can come in a variety of forms, from damaged equipment or downtime as a result of unplanned outages, to lost customers who expect reliable service.
Case Study 1:
When a production line suffers an unexpected power outage, it comes to halt. The cost of lost production time is obvious, but this cost can be compounded if unfinished products on the assembly line have to be thrown away or reprocessed.
Case Study 2:
Datacenter customers expect the highest level of uptime and reliability. When a power quality issue causes a data center to go down, their customers go down with them. Losses in revenue and customer trust trickle down and can cost millions, making the impact of any outage severe. Survey data suggests that power quality issues are now the number one leading indicator of power outages in data centers.
Protecting Both Sides of the Meter
The challenge of delivering high-quality power is not limited to utilities. Of the nearly $200 billion in annual losses, 80% of the power quality issues can be attributed to equipment or processes within the end user’s facility, not the commercial electricity provider.
Optical Sensors Enable Next-Generation Power Measurements
To identify a power quality issue, you need access to the right data. There are a variety of commercial-grade power metering solutions that can be used to measure electrical parameters such as energy, power, voltage, current, power factor, and frequency.
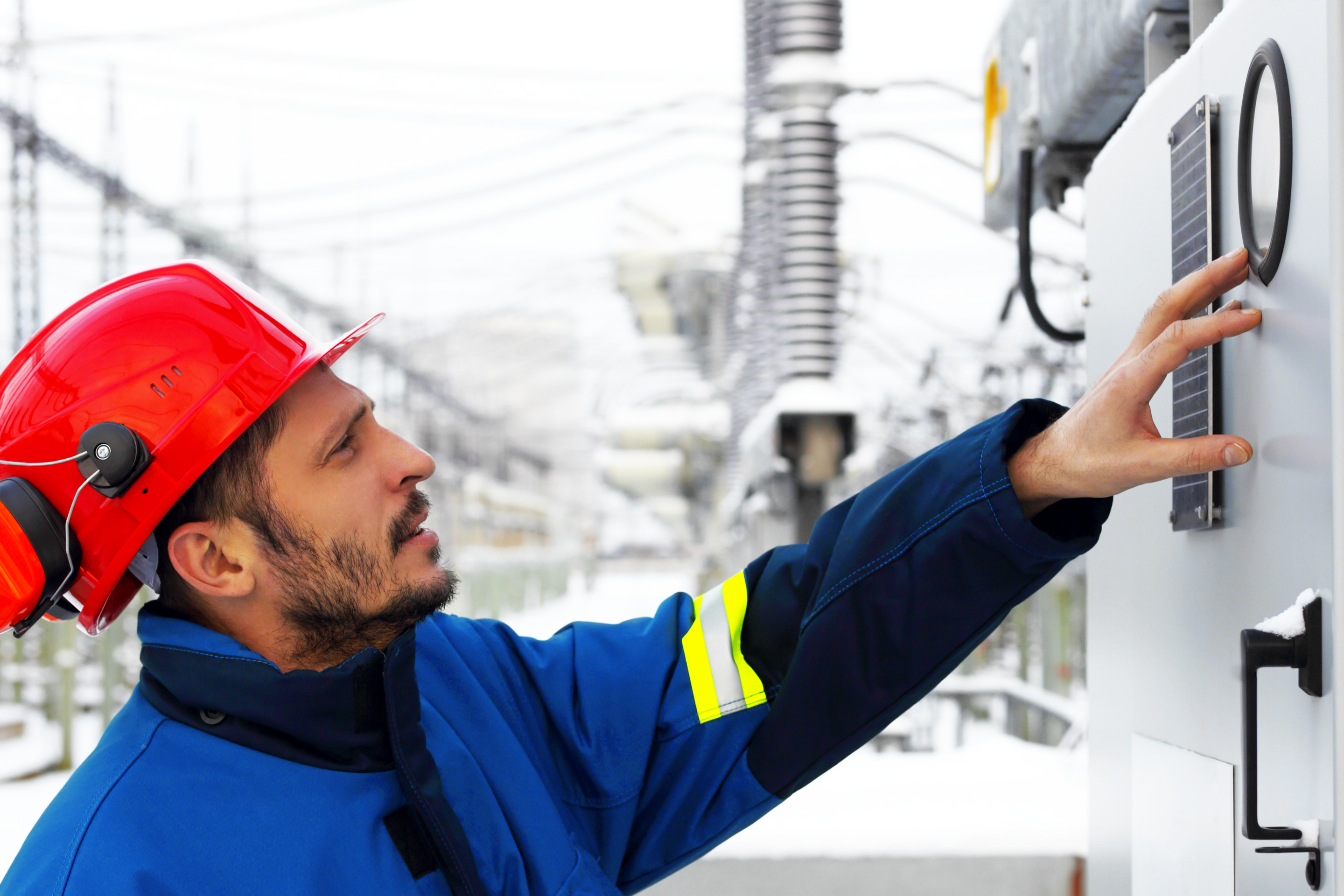
There are a few drawbacks to these solutions:
- They can be prohibitively expensive and complex to install.
- They are unable to detect the granular harmonic distortion issues required to protect highly sensitive electronic equipment.
- They do not provide data in real-time, where you need it, when you need it.
- They are part of the circuit and can therefore introduce safety concerns
A Better, Safer and More Affordable Way to Detect the “Ghost in the Machine”
MICATU’s Optical Sensor Platform is a game-changing technology, built to replace legacy measurement technologies. MICATU Optical Sensors can more safely measure everything PTs and CTs provide today, more accurately and with greater precision, and provide additional vital information that PTs and CTs cannot.
MICATU Optical Sensing Platform
Available Measurements
Power
Voltage
Current
Power Factor
Frequency
Phase Angle
Temperature
Total Harmonic Distortion
Accuracy & Precision
MICATU Optical Sensors have a sampling speed of 15,000 samples per cycle compared to only 32 samples per cycle of legacy solutions. This unlocks the capability to measure highly granular power quality data and achieve more accurate harmonics — to the 250th on voltage than the 11th on current measurements.
Real-time Data
All power quality data measured by MICATU’s Optical Sensing Platform is made available via DNP3 data points to your operational software systems in real-time with simultaneous analog outputs. You get the data you need, where you need it, when you need it, allowing you to be more proactive and armed to avoid the next outage.
Easy Installation
Modular and easy to install anywhere you need it, when you need it, with minimal or no interruptions to service. The m410B Optical Signal Processor enables setup with multiple sensor types.
Contact Us
Looking to transform the way you collect data from the grid? Our experts will help you upgrade your measurement technology for the grid of the future.